Content
- How To Treat Overhead Expenses In Cost Accounting
- Examples Of Activity Cost Drivers
- What Are The Issues Associated With Cost Tracing & Cost Allocation?
- How To Calculate Ending Inventory Using Absorption Costing
- 2 Describe And Identify Cost Drivers
- Cost Driver In Accounting: Definition, Analysis & Example
It measures, records and analyzes both fixed and variable costs for this purpose. The Activity Based Costing approach relates indirect cost to the activities that drive them to be incurred. Activity Based Costing is based on the belief that activities cause costs and therefore a link should be established between activities and product.Since electronics always seem to be in demand, you hope to have had great success with your new business. However, after about three months in business, you realize that the costs that you incurred are significantly higher than anticipated. These costs have begun to cut into your profits, and it’s time to figure out what’s happening. Is something that can be identified with a product, process, department, or a customer and can be tracked back to why the cost was incurred. Applied overhead is a fixed charge assigned to a specific production job or department within a business.For this reason, the selection of accurate cost drivers has a direct impact on the profitability and operations of an entity. When deciding which driver to use in terms of allocating indirect cost, consider the cause-and-effect relation between the cost and the driver. In addition, consider whether or not the cost driver activity is easily measurable.
How To Treat Overhead Expenses In Cost Accounting
Due to sophisticated manufacturing and increased demands from customers, direct labor is no longer the main cost driver of indirect manufacturing overhead. Management selects cost drivers as the basis for manufacturing overhead allocation. There are no industry standards stipulating or mandating cost driver selection. Company management selects cost drivers based on the variables of the expenses incurred during production.
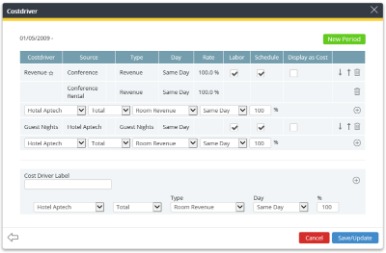
Before you can determine the cost driver, you must first locate the cost objects. These are the actual points of cost incurred and the activities that create the costs. For example, if you produce a product that requires hazardous material designations for transport, you will incur a fee to transport the materials on public roadways. Therefore, the total cost to produce item A is $1,100, and the total cost to produce item B is $1,400. While the above is a heavily-simplified example compared to a real-world situation, it shows the importance of allocating indirect costs to get a more accurate financial picture of a company. Increased levels of production would require more paint, more parts, and more workforce labor time to assemble.
Examples Of Activity Cost Drivers
Especially with larger and more complex businesses, cost drivers will always be an estimate. Activity cost drivers are specific activities that cause variable expenses to be incurred. One variable expense can comprise more than a single activity cost driver. For example, machine hours and labor hours can be activity cost drivers in the manufacturing of a product. The concept is most commonly used to assign overhead costs to the number of produced units. It can also be used in activity-based costing analysis to determine the causes of overhead, which can be used to minimize overhead costs.
- The correct allocation of manufacturing overhead is important to determine the true cost of a product.
- Cost drivers are essential in ABC, a branch of managerial accounting that allocates the indirect costs, or overheads, of an activity.
- These unnecessary cost drivers ultimately drive down the margins and revenue produced.
- In addition, consider whether or not the cost driver activity is easily measurable.
- These are the necessary expenditures and can be fixed or variable in nature like the office expenses, administration, sales promotion expense, etc.
- An activity cost driver, also known as a causal factor, causes the cost of an activity to increase or decrease.
- Traditional costing methods allocate indirect costs to production activities based on volume of output.
A large number of cost drivers may be used within an activity-based costing system. If a business is only concerned with following the minimum accounting requirements to allocate overhead to produced goods, then just a single cost driver should be used.
What Are The Issues Associated With Cost Tracing & Cost Allocation?
Harold Averkamp has worked as a university accounting instructor, accountant, and consultant for more than 25 years. He is the sole author of all the materials on AccountingCoach.com. Peggy James is a CPA with over 9 years of experience in accounting and finance, including corporate, nonprofit, and personal finance environments. She most recently worked at Duke University and is the owner of Peggy James, CPA, PLLC, serving small businesses, nonprofits, solopreneurs, freelancers, and individuals. Zach Lazzari is a freelance writer with extensive experience in startups and digital advertising. He has a diverse background with a strong presence in the digital marketing world.
What is pocket cost?
Definition: Out of pocket costs in managerial accounting are expenses that could be incurred or avoided depending on management’s decisions. In other words, an out-of-pocket cost is a potential future outlay of cash that management needs to decide whether or not to make.For example, an indirect or variable cost may be relevant at the unit level, the batch level, the product level, the customer level, or the facility level. Once you determine the appropriate hierarchical level, choose a cost driver activity at that level in order to allocate the indirect or variable cost. Activity-based costing is an accounting method that allocates both direct and indirect costs to business activities. An activity cost driver, also known as a causal factor, causes the cost of an activity to increase or decrease. An example is a change in the cost of warehousing or a change in the level of production. This fee is the cost object, and it is difficult to distribute that cost across the business, as it fluctuates, based on the level of production and transportation activity. The activity changes your overhead and acts as a cost driver that adjusts the cost of production and bringing the product to market.
How To Calculate Ending Inventory Using Absorption Costing
As technology changes, however, the mix between materials, labor, and overhead changes. Often, improved technology means less waste of material and fewer direct labor hours, but possibly more overhead.
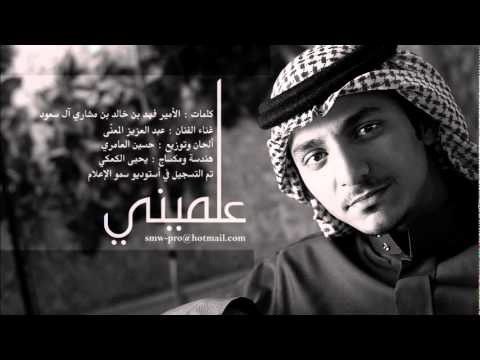
Allocating cost drivers appropriately is important in accurately determining the cost of producing a good or service, as well as making financial projections. A cost driver simplifies the allocation of manufacturing overheads, such as the costs of factory space and electricity.In accounting, the cost driver definition is a factor that incurs cost. Use cost drivers to allocate variable and indirect costs to production activities or output.
2 Describe And Identify Cost Drivers
It provides a competitive edge to the business as they give a precise distribution of cost based on activities performed. Increases, it can cause the cost of producing a product to also increase. Sales and all related variable expenses are often the driver for commissions, bad debt, insurance expense, and so on.
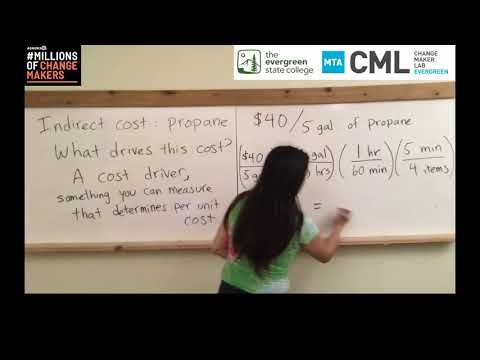
The cost drivers thus are the link between the activities and the cost of the product. When a factory machine requires periodic maintenance, the cost of the maintenance is allocated to the products produced by the machine. After every 1,000 machine-hours, there is a maintenance expense of $500. Therefore, every machine hour results in a 50 cent (500 / 1,000) maintenance cost allocated to the product being manufactured based on the cost driver of machine-hours. Each machine is capable of producing a specific number of units in a given time period. To grow that number, additional machinery must enter the cost driver equation. The actual production and final product inspection are also common activity drivers that effect costs.These costs are almost always recurring and necessary to operate the production side of the business. A cost driver simplifies the allocation of manufacturing overhead. The correct allocation of manufacturing overhead is important to determine the true cost of a product. Internal management uses the cost of a product to determine the prices of the products they produce.
Cost Driver In Accounting: Definition, Analysis & Example
It is also necessary to consider the cost behavior of the relevant cost. The relevant cost refers to the cost’s response to the activity of the driver. In addition, approximate the relationship between costs and cost drivers using regression analysis. Most cost drivers simply cannot be eliminated, without having a serious effect on the business. The production process is one area where technology is naturally influencing the activity-based costing formula however.
What’s The Difference Between Prime Costs And Conversion Costs?
An indirect or variable cost may have several possible cost drivers. Traditional costing methods allocate indirect costs to production activities based on volume of output. Conversely,activity-based costing allocates indirect costs to particular production activities related to that cost.Overhead refers to the ongoing business expenses not directly attributed to creating a product or service. Explain why it is necessary to use preliminary stage and primary stage cost drivers. You soon realize that a particular brand of car stereos have had an abundance of returns, because the volume button does not work well. It was at that time that you also realized that those returns have become a cost driver. Download the free Know Your Economics guide to easily manage the factors incurring costs in your company.For instance, the painting process would be split into its own cost pool including activities like bodywork, sanding, buffing, and spraying. A cost driver for the painting department might be the increased wages in accordance with the new union agreement. Since preparing car bodies is a fairly labor intensive operation, an increase in wages can drastically increase the cost of theactivity. Automation is essentially taking the production activity-based costing and removing the human element.