Content
- Production Costs Vs Manufacturing Costs: What’s The Difference?
- Photovoltaic System Design
- Production Costs Vs Manufacturing Costs: An Overview
- What Is Direct Labor?
- How To Calculate Total Manufacturing Cost
- Manufacturing Cost
The value of offsetting greenhouse gas emissions is increasingly being considered in cost–benefit analysis. For example, a 1-kW-rated PV system on the East Coast of the United States will produce energy equivalent to burning about 44 tonnes of coal during a 30-year lifetime. The emission of about 21 tonnes of CO2, 64kg of SO2, and 31kg of nitrogen oxides will also be avoided. National Park Service estimated emissions credits of $15/tonne ($14/ton) for CO2, $1.65/kg ($0.75/lb) for SO2, and $7.49/kg ($3.40/lb) for NOx.
How do you calculate labor manufacturing costs?
Calculate the direct labor hours The figure is obtained by dividing the total number of finished products by the total number of direct labor hours needed to produce them. For example, if it takes 100 hours to produce 1,000 items, 1 hour is needed to produce 10 products and 0.1 hours to produce 1 unit.The sample part on the platform is in its biggest area 15 mm x 15 mm and split into 14 different steps, which will help to determine the overall build speed. This size has been chosen as all currently used layer thickness (0.25 μm /0.3 μm /0.5 μm ) can achieve this height.
Production Costs Vs Manufacturing Costs: What’s The Difference?
Your manufacturing facility incurs expenses whether you are manufacturing or not. These costs include utilities, rent or mortgage payments, depreciation on equipment and security. You should pay close attention to your overhead expenses and analyze how much they contribute to the cost of manufacturing.These expenses stay the same regardless of the level of production, so per-item costs are reduced if the business makes more widgets. Costs of production include many of the fixed and variable costs of operating a business. Product costs are costs necessary to manufacture a product, while period costs are non-manufacturing costs that are expensed within an accounting period. When looking at total manufacturing cost, you might not only learn that the materials being bought are too expensive, but also that too many materials are being bought in the first place. By analysing the amount of excess that is usually generated during production, you can use this to adopt a more sparing approach to purchasing. In addition to the three most common manufacturing costs, you have expenses for supplies such as tools, tape, lubricants and safety gear.
- Calculated MSP and manufacturing cost breakdown for a 20MWe geothermal steam turbine in different volumes of manufacturing in the United States.
- The calculation for total manufacturing cost involves a detailed accounting for the costs of materials, labor and overhead.
- But the problem with this is that Austin already has state-of-the-art tools, computer hardware and software, warehousing, and all other necessary supplies.
- Brian Beers is a digital editor, writer, Emmy-nominated producer, and content expert with 15+ years of experience writing about corporate finance & accounting, fundamental analysis, and investing.
- The generator is a separate piece and is not included in the manufacturing cost analysis.
For example, the bamboo around the village may disappear if a lot is used, so you may have to buy from other villages to use. To ensure a continuing supply of natural resources to be used in the future, everyone should help to conserve environment and natural resources by replanting the resources.The profitability picture gained from total manufacturing cost will also govern other strategies too, such as your approach to sales and pricing. If your profits are not at the desired level, you may determine that the current sales model isn’t working and that you perhaps need new methods or to open new sales streams (such as e-commerce).
Photovoltaic System Design
Japan and Germany currently lead the United States in world production. U.S. production was about 75MWpk in 2000, with more than 70% of the production being exported for cost-effective international applications. A lot of the ‘value’ of cost analysis, therefore, is in the way that it can make relative comparisons between different designs or manufacturing methods. It may also shine a light on costs that have, over time, become extortionate without you realising.
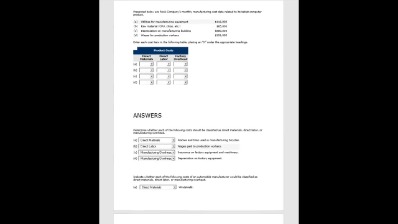
To find the manufacturing cost per unit formula, simply divide the above results by the number of units produced. The opportunity to achieve a lower per-item fixed cost motivates many businesses to continue expanding production up to total capacity. Manufacturing costs, for the most part, are sensitive to changes in production volume. Note 1.43 “Business in Action 1.5” details the materials, labor, and manufacturing overhead at a company that has been producing boats since 1968. The costs of workers who are involved in the production process but whose time cannot easily be traced to the product. Labor performed by workers who convert materials into a finished product and whose time is easily traced to the product.This not only has financial benefits but improves your environmental standing too . By having less produce in the warehouse at any given time, fewer storage costs are incurred, and your facility is far more organised as a result. There are some well-known stock control strategies that can be utilised to achieve these outcomes. Many explain manufacturing cost as the cost to bring a product from raw material to the point where it can be sold. A variable cost is an expense that changes in proportion to production or sales volume. Both of these figures are used to evaluate the total expenses of operating a manufacturing business. The revenue that a company generates must exceed the total expense before it achieves profitability.
Production Costs Vs Manufacturing Costs: An Overview
This newfound visibility around spend could lead to a renegotiation with suppliers, to attain cheaper deals. Or you may research some other potential partners, who can provide you with a better price . Kevin Johnston writes for Ameriprise Financial, the Rutgers University MBA Program and Evan Carmichael. For example, Austin is the CEO of a plant which manufactures home appliances. Although Austin is experienced in his trade, he has used the experiences former managers have passed on to create a profitable company.Full costing is a managerial accounting method that describes when all fixed and variable costs are used to compute the total cost per unit. Note 1.48 “Business in Action 1.6” provides examples of nonmanufacturing costs at PepsiCo, Inc.
What Is Direct Labor?
Once you understand the three major expenses, you can move on to other more-subtle cost considerations. Consider an example of calculating manufacturing costs for Flying Pigs Corporation and the company’s costs to make roller skates. Manufacturing businesses calculate their overall expenses in terms of the cost of production per item. That number is, of course, critical to setting the wholesale price of the item. Manufacturing costs are the expenses directly related to building the product. Identify whether each item in the following should be categorized as a product cost or as period cost.Manufacturing costs at 15% IRR rise to about $26.00 per barrel, adding an additional $12.00 per barrel to the expected minimum, or break-even, manufacturing cost. As further illustrated, this 15% IRR likely is achievable in an $18.00 per barrel crude oil market. At an 8% IRR, manufacturing costs rise to only $18.00 per barrel.
What are the five cost concepts?
Accounting costs and Economic costs. Outlay costs and Opportunity costs. Direct/Traceable costs and Indirect/Untraceable costs. Incremental costs and Sunk costs. Private costs and Social costs.Removing steps from the production process to save money also increases efficiency, ensuring that items are created faster . Manufacturers that don’t possess an accurate picture of spend will often have a distorted perception of their financial health, which could cause them to budget poorly. Total manufacturing cost, when compared with income and revenue, provides clarity around profitability and overall business performance. With regards to indirect labour costs, this would be the wages paid to employees that weren’t physically involved with manufacturing, but still played some part in the process. If your small business engages in manufacturing, you should know three common manufacturing expenses. Many business owners make the mistake of estimating profits based on one manufacturing expense and are surprised when actual numbers come in.
How To Calculate Total Manufacturing Cost
After subtracting the manufacturing cost of $10, each widget makes $90 for the business. Quality Management Systems can completely reshape a company’s total manufacturing costs for the better. Manufacturing overhead, which includes all of the other costs incurred in the manufacturing activities. These indirect costs include repairs and maintenance, depreciation of the manufacturing equipment, utilities, salaries of manufacturing supervisors, etc. Both production costs and manufacturing costs must be included in the calculation of the per-item cost of doing business.
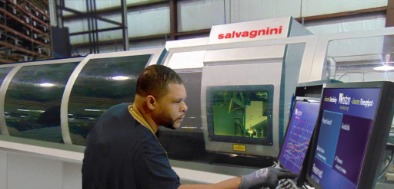
Effectively, a standard steam turbine design, even at low manufactured volumes, could save approximately 63% of the steam turbine $/kW. This is determined by comparing the income with manufacturing costs.•It makes several assumptions about the speed and efficiency with which manufacturing activities are done. Obviously, such assumptions should be kept constant throughout a costing analysis to keep the results in balance.
How To Calculate The Total Manufacturing Cost In Accounting
Indirect labor includes the production supervisors who oversee production for several different boats and product lines. The manufacturing cost of a custom design 5MW ORC turboexpander is only $187,000 more than that of a custom design 1MW ORC turboexpander. This shows that the size of the turbine does not have a significant effect on the total cost of the turbine/turboexpander. Defined as the labor, material, and overhead costs in producing a finished product, manufacturing costs are the most significant factor in any manufacturing business.